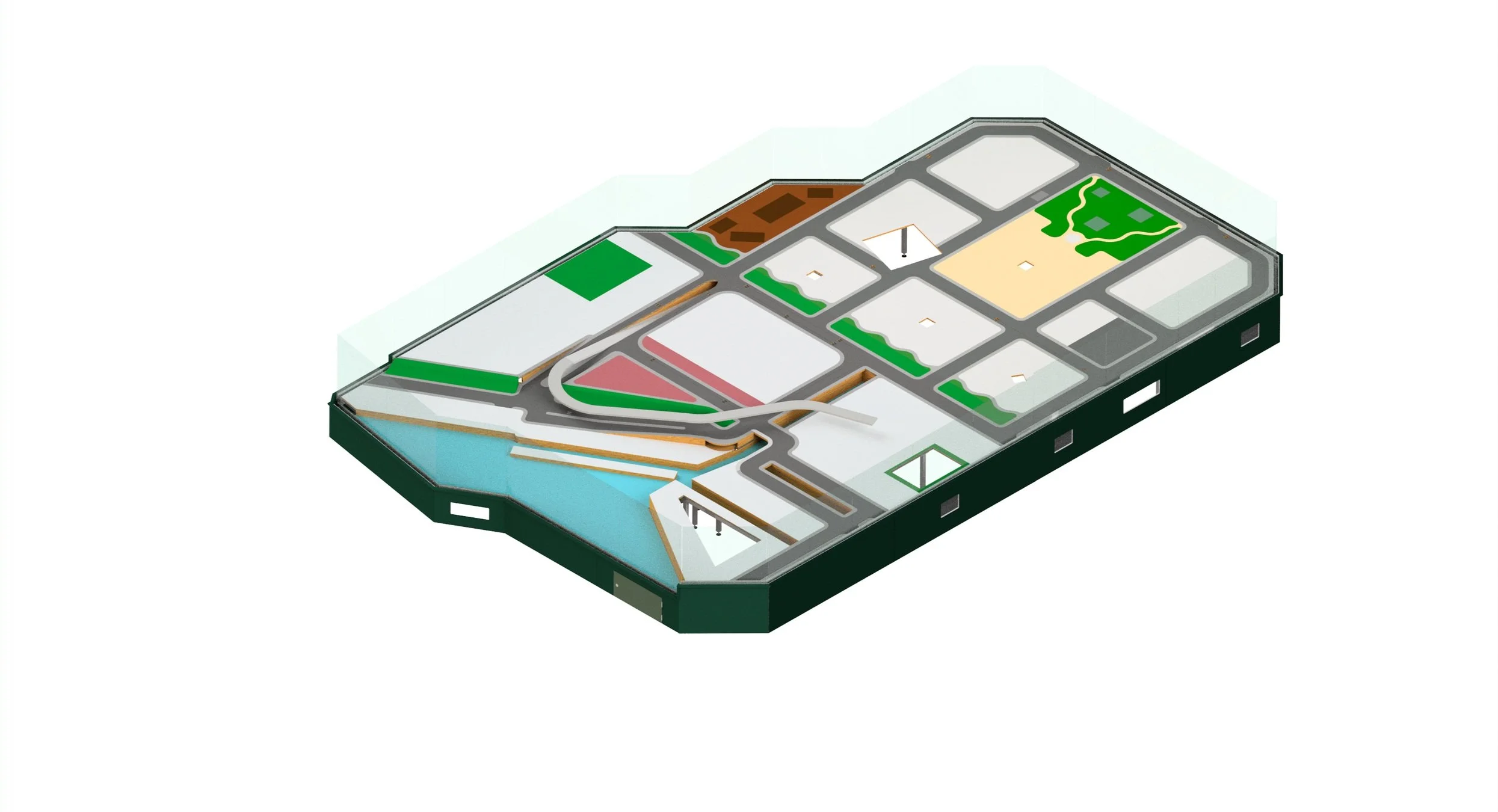
Layout Design
As a technical designer for Merlin Entertainments, I am experienced in creating podium layout designs of an indoor LEGO attraction - translating a layout render into a manufacturable model and 2D drawing to be sent to contractors.
To complete this task I required proficiency in Rhino, Fusion 360 and Autodesk Inventor. The physical, outer, appearance of the attraction originated from the Rhino file, which provided sizing limits and the location of LEGO animatronics which would effect how podiums are split into smaller, manufacturable boards. Working from the Rhino file and Fusion 360 models of technical effects, I was solely responsible for calculating and designing supporting steel frames; glass panels; surface MDF and plywood boards; and side MDF wall panels to be handed over to contractors to manufacture.
This required design for manufacture skills, attention to detail, and collaboration across departments, as to improve the ease of manufacture and installation.
LEGO Discovery Centre
I was solely responsible for designing the central podium for manufacture for an overseas LEGO indoor attraction.
The final layout design - I modelled the podium in Autodesk Inventor, exporting back to Rhino to import LEGO models and create the video view.
Design Process
The Rhino model was split strategically into smaller panels for ease of manufacture. This was modelled in Autodesk Inventor, where I utilised off-the-shelf MDF/Plywood sizing and designed a ‘standard’ steel support frame to be used wherever possible. Standardising sizes, whether for steel frames or wall and glass panels helped minimise costs, as fewer drawings and deviations of parts needed to be made.
Multi-tasking, problem solving, and attention to detail was necessary to ensure that all components could be assembled together and not impede the difficulty of install. For example, steel frames were adjusted where necessary to avoid openings for LEGO content and door access to underneath the podium. Similarly, frame legs were placed as to allow efficient movement of car creepers underneath the podium - in which colleagues and I worked on during install to travel faster with tools to install effects.
Following a design review, 2D design packs were created for every element of the layout, i.e. glass, steel, ect., to send to different contractors - improving speed of manufacture of the podium within a tight deadline.
The original Rhino file I started work from - providing the LEGO surface content. Surfaces are not split and modelled for manufacture, nor is there any detail under the podium.
Installation
My 3D model and 2D drawings were used by contractors to manufacture and build the central podium within the overseas LEGO Discovery Centre. Each section the podium was split into was labelled alphabetically in a top-down approach. This helped the speed of the build stage by reducing the likelihood of parts being installed in wrong sections of the podium.
I was part of the install tech team for this attraction - where I installed LEGO animatronics and all cabling to run the effects and lighting. As a result I have experience working with contractors both remotely and overseas on-site - where I am confident in my communication and project delivery skills.